IMC distributes Mason Color®’s cobalt aluminate.
Investment cast super-alloys may require surfaces with specially controlled grain sizing. The most common means of obtaining these critical grain specifications on the surface is by incorporating nucleating compounds such as cobalt aluminate in the prime dip coat. Some foundries, including grey iron (sand casting), occasionally paint their moulds at points of stress with a slurry of a nucleating compound such as cobalt aluminate. It is reported that this tends to reduce cracking.
The following chart shows the most used nucleating compounds and their main components.
Properties | 6330 Cobalt Aluminate | K-4704 Cobalt Aluminate | K-4538 Meta-Silicate |
---|---|---|---|
Cobalt (range) | 39-41,5 % | 30,5-33 % | 40,5-44 % |
Acid-soluble soda (max) | 0,4 % | 0,4 % | 0,35 % |
CaO (max) | 0,05 % | 0,05 % | 0,05 % |
Fe (max) | 0,04 % | 0,06 % | 0,04 % |
MgO (max) | 0,05 % | 0,05 % | 0,04 % |
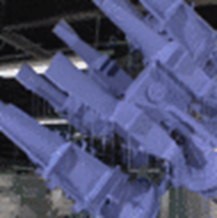
Contact us with your questions on prime and backup coat composition. We look forward to helping you in any way we can.
The Latex proposed by IMC is a water-based non-ionically stabilized hydrolysis-resistant dispersion of a carboxylate styrene-butadiene copolymer. It contains an antioxidant and is compatible with most hydraulic binders. This product has been designed particularly for applications like industrial flooring screeds.
Property | Value | Unit | Method* |
---|---|---|---|
Total Solids | 47.0 | % | ISO 3251 |
pH | 10.0 | ISO 976 | |
Viscosity (Brookfield LVF, 60 rpm) | 90 | mPas | ISO 1652 |
* Internal method based upon the specified norm
Our supplier Nalco® will be able also to offer a proprietary polymer designed for use with colloidal silica binders in primary and backup slurry formulations. They are formulated to optimize slurry rheology for uniform coverage, resulting in better surface detail, fewer breakouts due to poor coverage, and better retention on part edges.
You will find the typical values of Polymer offered by Nalco® below.
Typical Value | HP Polymer | ESP 6300 | ESP 6305 |
---|---|---|---|
Total Solid (%) | - | 50.0-52.0 | 49.5-52.0 |
Viscosity @ 77°F/25°C | - | 100-400 | - |
pH (@ 77°F/25°C) | 8.35-9.00 | 8.4-9.2 | 8.35-9.00 |
Contact us with your questions on prime and backup coat composition. We look forward to helping you in any way we can.
IMC’s offerings include a wetting agent as an addition to your slurry: a non-ionic non-foaming non-toxic biodegradable organic wetting agent that is effective with both acidic and alkaline binders used in the investment casting process.
The product should be added to primary slurries at an initial 0.25% (v/v) level, based upon total binder liquid (binder plus concentrate plus any dilution water).
Since waxes vary in their wettability, the slurry should be checked regularly to make sure that it is properly wetting the wax patterns.
If more wetting property is needed, the wetting agent should be added in 0.05% (v/v) increments until satisfactory wetting is achieved. Normally, it should be used at levels below 0.75% (v/v).
This product, like other wetting agents, should be used in conjunction with an effective antifoam.
IMC’s offerings include an antifoam that provides long-term effectiveness in water-based investment casting slurries. The product was formulated to prevent casting defects due to bubble formation during slurry drainage.
It is a blend of silicone and polyglycols in a hydrocarbon solvent.